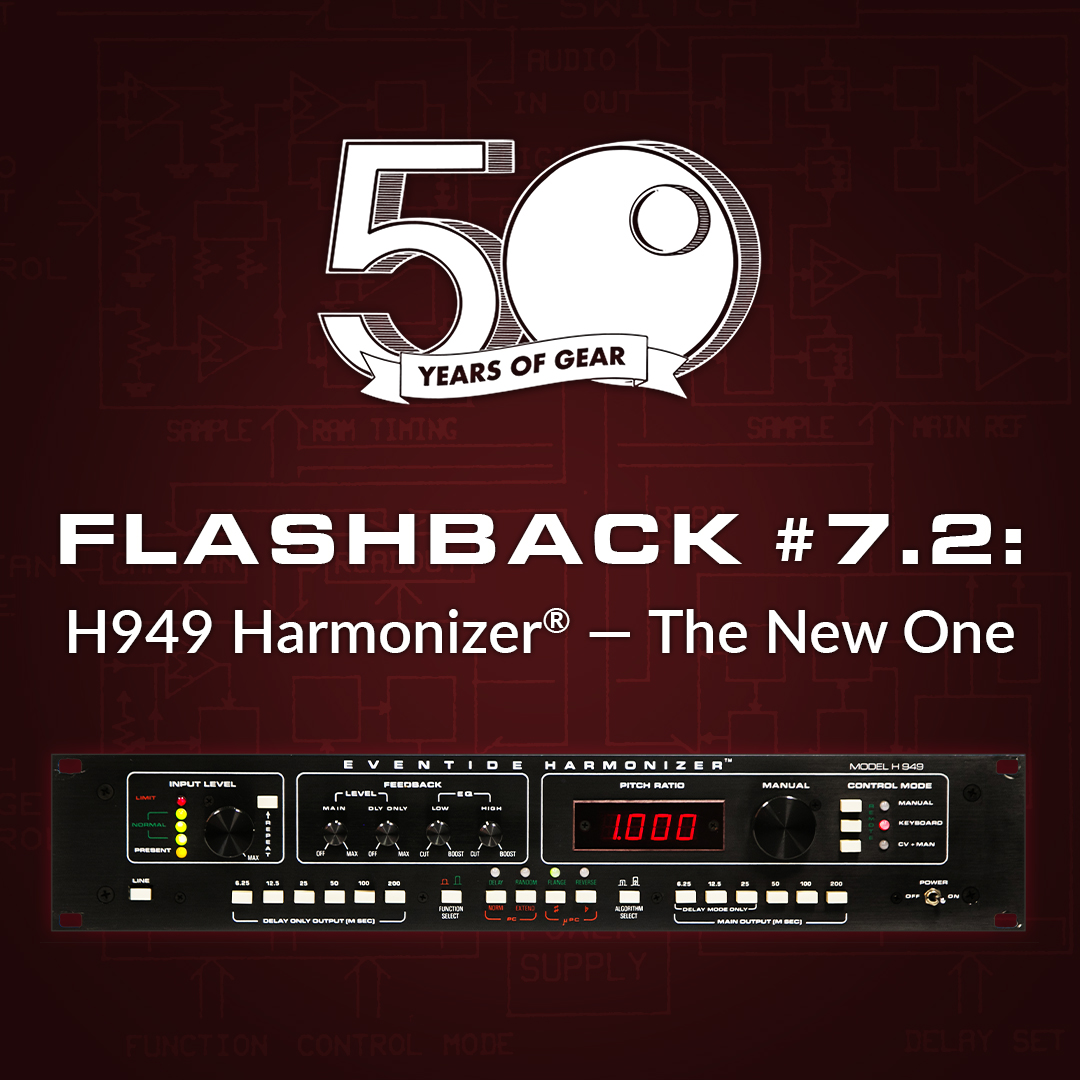
Flashback 7.1, “Ding Dong! The Glitch is Dead,” took a deep dive into the technology at the heart of de-glitching pitch change, an advance that made tuning pitchy voices and instruments practical for the first time. Now, let’s return from our ramble down Nerd Boulevard and learn some of the other reasons why so many H910 fans sprung for over $11,000 (in 2021 dollars) to buy an H949 as soon as it hit the market. The H949 greatly expanded the sonic horizon of the simpler H910. The rapid advance of technology made improvements impossible to resist and new features possible to imagine. Plus, we had the benefit of users’ suggestions and pleas.

The H910’s designer, Tony Agnello, knew what he wanted and needed to do next. Some things were obvious, others less so. To accomplish some of the ideas he had in mind, his first step was to design a compute engine that could generate as many memory addresses as possible for each audio sample. By designing a primitive yet really fast address computation machine, the H949’s design made possible unprecedented digital muckery, as implied by the front panel control legends:
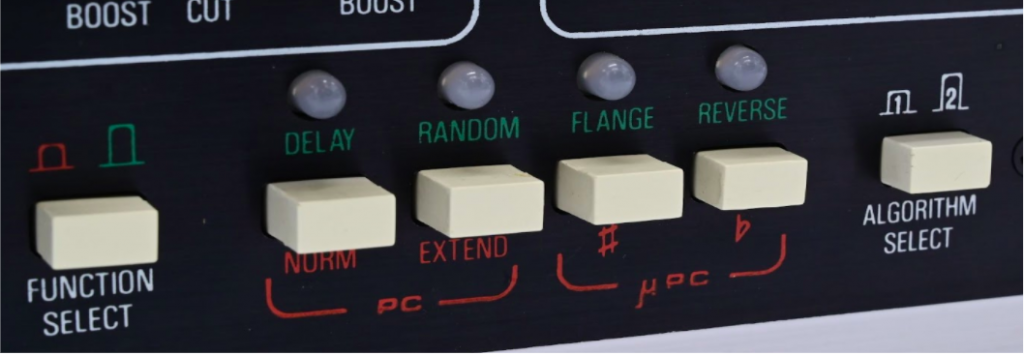
It had a ‘FUNCTION SELECT’ button and some unusual labels—‘RANDOM,’ ‘µ PC,’ ‘EXTEND,’ and ‘ALGORITHM’—screened on the front panel. (And, who’s “NORM”?)
So New, So Cool
In 1980, Suzanne Ciani demonstrated her “Voice Box, ” which featured an H949, to the amusement and bemusement of David Letterman and his national audience:
Strange & Confusing?
The User Guide acknowledged, upfront, that the “model H949…may seem confusing at first” and included a list of “things which may seem strange,” but offered reassurance that they were “THINGS NOT TO WORRY ABOUT.”


The Obvious Next Steps
More Memory, Longer Delay
The H910 used the highest density memory chips available at the time, 4k-bits, which yielded a maximum delay of 100 msec. The H949 took advantage of new 16k-bit RAMs to deliver nearly a half-second of delay.
How Low Can You Go?
The H910 was a two-octave pitch changer—one octave up, one down. The H949 added a third octave of pitch change—one octave up, two down.
One More Bit, Four Thousand More Hertz
The H949 audio specs surpassed those of the H910 with a 96 dB dynamic range vs. the H910’s 90 dB range, and a frequency response flat to 16 kHz vs. 12 kHz.
Input Level Metering
The first LEDs were red only. Yellow and green followed a few years later and we used them to add an input level “meter.” Early analog-to-digital converters had limited dynamic range and setting signal level was critical. In the heat of the distortion vs. noise battle, blinking lights help (and add a bit of festivity).
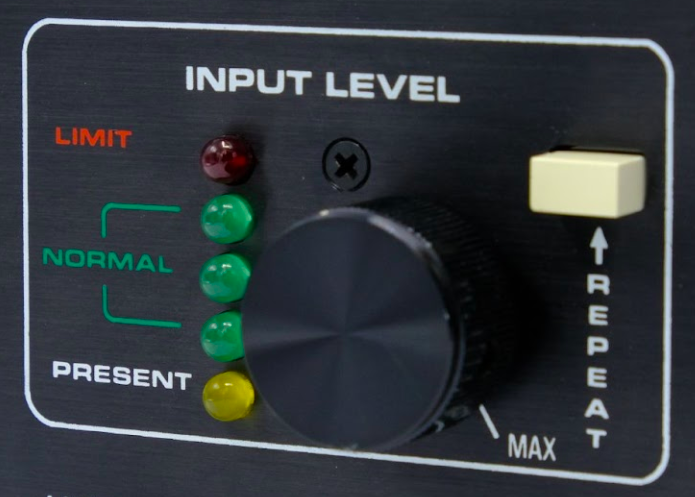
Just One More Bit
The H910’s specified dynamic range was 90 dB, remarkable at a time before integrated A/D converters existed. The designers of early digital audio products were forced to design their own converters. The standard approach was a technique called ‘successive approximation’ which used digital-to-analog converter chips. Eventide eschewed this common approach because it became noisy at small signal levels. At Federal Scientific Corp, his previous place of striving, Richard Factor had learned of an approach that guaranteed monotonicity, the ‘run down’ converter, also used in our earlier DDLs. This method of conversion required an extremely high-speed clock and the latest, fastest logic chips available at the time, ECL (Emitter Coupled Logic). The H910’s analog-to-digital converter yielded 10 bits of resolution, which entitles one to 60 dB of dynamic range, theoretically 6 dB per bit. When the H949 was designed, newer ECL chips ran twice as fast as the chips in the H910. Doubling the master clock frequency yielded an additional bit of resolution and a theoretical 11-bit dynamic range of 66 dB.
Still, 66 dB isn’t good enough for the pro-audio user. To meet pro-audio specs, all of Eventide’s early digital products used DBX modules designed by Dave Blackmer. They compressed the audio input signal by a 2:1 ratio on the way to the A/D and expanded it by 1:2 on the way out.
Screwdriver-Free Audio I/O Connection
Eventide’s first rack-mount products weren’t designed to plug audio in, but rather required users to wire them in. Audio I/O on the H910, the Omnipressor®, and the Instant Phaser was via a ‘terminal strip,’ which required stripped cables and a screwdriver.
The Somewhat Obvious Next Steps
MicroPitch
Engineers used the H910 for double-tracking by making tiny pitch changes, so Tony decided that the H949 would have a dedicated “MicroPitch” mode. Being both geeky and Greeky, he labeled it µPC to fit the limited space. The H910 had a three-digit LED display and 1% pitch resolution. The H949’s display added a fourth digit to support its 10X resolution compared to the H910. With 0.1% pitch resolution, the H949 became useful as an instrument—a precision tool for tuning and tempo control. In addition to making MicroPitch a ‘go-to’ technique, for the first time, engineers could fix sharp/flat vocals and guitars.
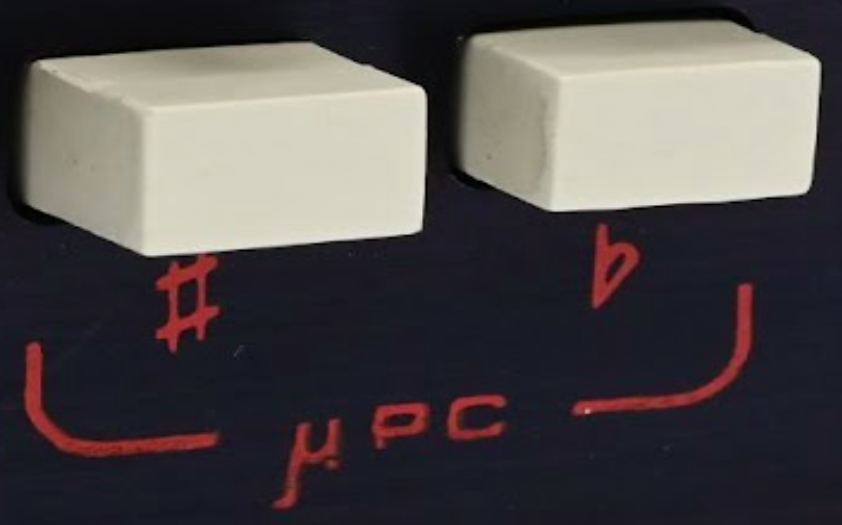
Reverse
Before digital audio, reversing audio was only possible using mechanical devices like tape machines and vinyl players. The H949’s Reverse mode was analogous to cutting tape into 6-inch segments (~400 msec), reversing each segment, and then splicing each reversed segment in the original order. Today, these segments would probably be called ‘grains.’ Pitch Control was active in Reverse mode so that the user could change the pitch of the reversed segments. Combined with the ability to feedback around the reversed, delayed, and pitch-changed segments, all sorts of new sounds became possible. Consider that feeding back a reversed signal through the reverse process would make the segment ‘forward’ again (in a totally fortuitous way). The user even had control over the granularity or segment length, down to as little as 50 msec.
Repeat/Capture
Like our first DDLs, the H949 had a Repeat function. We used the term Repeat from day one, but, in retrospect, Capture may have been a better word. Given the fact that the first delays had a maximum delay of 200 msec, Repeat seemed appropriate at the time. The H949’s Repeat function broke new ground by having the ability to both time-reverse and pitch-change the ‘captured’ audio.
Flange Mode
By including a Flange Mode, the H949 was recognized as one of audio’s first “multi-effects’ products. The ability to combine flanging with delay and feedback by twisting a few knobs on a single device made it all too easy to create both sonic bliss and malfeasance. You’re welcome!
Feedback: Double Your Fun and Add EQ, Too!
Like the H910, the H949 had a monaural input with dual outputs. The main output was capable of the range of effects already discussed, while the secondary output was limited to delay only. The H910 had a one-knob feedback control, and we found that users would sometimes patch an equalizer into the feedback path. The H949 sported built-in EQ and a control for feeding back the Delay Only output for a greater range of feedback effects.
Reverse
Before digital audio, reversing audio was only possible using mechanical devices like tape machines and vinyl players. The H949’s Reverse mode was analogous to cutting tape into 6-inch segments (~400 msec), reversing each segment, and then splicing each reversed segment in the original order. Today, these segments would probably be called ‘grains.’ Pitch Control was active in Reverse mode so that the user could change the pitch of the reversed segments. Combined with the ability to feedback around the reversed, delayed, and pitch-changed segments, all sorts of new sounds became possible. Consider that feeding back a reversed signal through the reverse process would make the segment ‘forward’ again (in a totally fortuitous way). The user even had control over the granularity or segment length, down to as little as 50 msec.
Repeat/Capture
Like our first DDLs, the H949 had a Repeat function. We used the term Repeat from day one, but, in retrospect, Capture may have been a better word. Given the fact that the first delays had a maximum delay of 200 msec, Repeat seemed appropriate at the time. The H949’s Repeat function broke new ground by having the ability to both time-reverse and pitch-change the ‘captured’ audio.
Flange Mode
By including a Flange Mode, the H949 was recognized as one of audio’s first “multi-effects’ products. The ability to combine flanging with delay and feedback by twisting a few knobs on a single device made it all too easy to create both sonic bliss and malfeasance. You’re welcome!
Feedback: Double Your Fun and Add EQ, Too!
Like the H910, the H949 had a monaural input with dual outputs. The main output was capable of the range of effects already discussed, while the secondary output was limited to delay only. The H910 had a one-knob feedback control, and we found that users would sometimes patch an equalizer into the feedback path. The H949 sported built-in EQ and a control for feeding back the Delay Only output for a greater range of feedback effects.
The Not-So-Obvious Next Steps
While technology’s rapid advance made some of these next-generation features rather obvious, the H949 also introduced some concepts that were entirely new.
Algorithms
With the H949, Eventide introduced the pro-audio world to the concept of the “algorithm.” The front panel “Algorithm Select” button gave engineers two options for splicing pitch-changed audio. Flashback #7.1 told the tale of the Glitch.

Random Mode
The H949 offered a new concept that was a bit of a puzzle to the average user—random delay. Here’s how Random Mode was described in the User Manual:
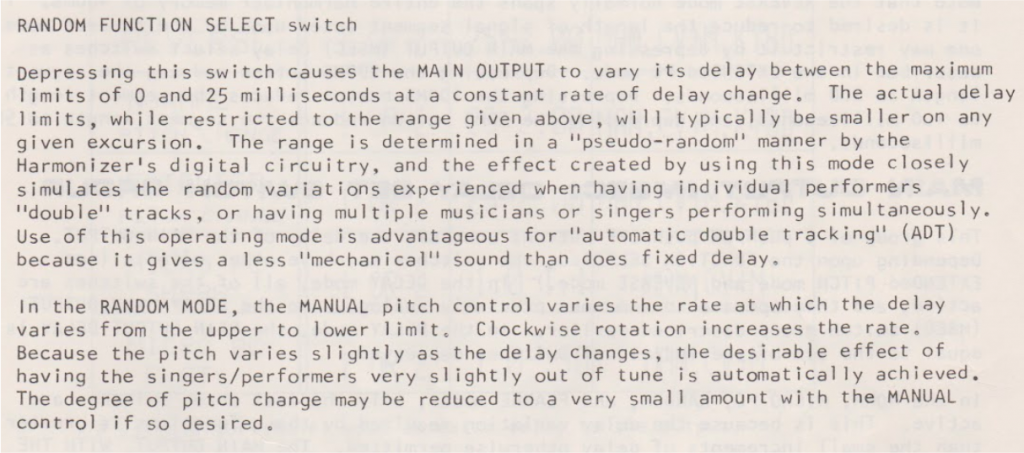
Extended Delay Mode
OK. Admittedly, the term “Extended Delay” needs explanation. Even today, it’s hard to come up with a legend that clearly indicates what this function does; it’s really about latency. Extended Delay Mode gave the user additional control of the pitch change algorithm, which normally used a ~25 msec segment of memory to achieve pitch change. The H910 and H949 were designed to be used in real-time and limited the maximum delay to 25 msec in order to keep latency low. Extended mode allowed the algorithm to increase the segment of audio used for pitch change to 400 msec. Using longer segments resulted in less frequent splicing. The combination of maximally extended delay, the gentle splicing of Algorithm 1, and just the right amount of feedback created a decidedly sea-sick feel.
FX Aside—A Precision Audio Tool
But, the H949 was more than just a digital FX box. It was a precise digital audio instrument that could be used for manipulating time itself…
The Three Fs
Professor Alex Case describes the “Three Fs” of audio processing as Fix, Fit, and Feature. Engineers first use tools to ‘Fix’ problems, then ‘Fit’ things together, and finally, and only then, go for wacky ‘Features.’ The H949 was one of the first devices to pull off the ‘hat trick’ by checking off all three boxes. With its combination of fine pitch resolution and de-glitching intelligence, the H949 was used by studio engineers to “Fix” pitchy tracks. Its combination of two channels of delay and slight pitch change allowed engineers to better “Fit” a track into the stereo mix. And, definitely, in both the studio and on stage, musicians and engineers dramatically used the H949 to “Feature” tracks. Prof. Case uses the term “Fit” to mean modifying the sound of a track to make it ‘Fit’ better in the jigsaw puzzle of the multitrack arrangement. But, apart from that sense of the word, the H949 was also used to literally fit complete program material into a defined time slot! Many of our early customers were broadcast engineers who used the H949 to leave pitch unaffected while changing the running time of program material.
TimeSqueeze
We were giddily aware that broadcast engineers were using the H910 to “Fit” audio into shorter time slots to sell more ad time. Broadcasters helped float the good ship Eventide back then as they do still today (we’ll go in depth on our Broadcast Delay units in a later Flashback). A unique broadcast-oriented feature of the H949 was a built-in capstan drive. Capstan was and is a nautical term, borrowed by the tape-recorder industry. It was usually the shaft of a precision motor that protruded through the tape deck and regulated the speed of the tape.
Capstan Drive
By the late ‘70s, many studios had Varispeed drive units that controlled the speed of the capstan motor. The H949 could, in turn, control the Varispeed so that a track’s tempo would change while reciprocally adjusting the pitch. Just turn the big knob, dial in 0.900, the tape would be sped up by 11%, and voila, the pitch would be unaltered! Back then it was quite an experience to turn the knob on a rack-mount effects device and watch the reels of the tape machine speed up and slow down precisely to maintain pitch.
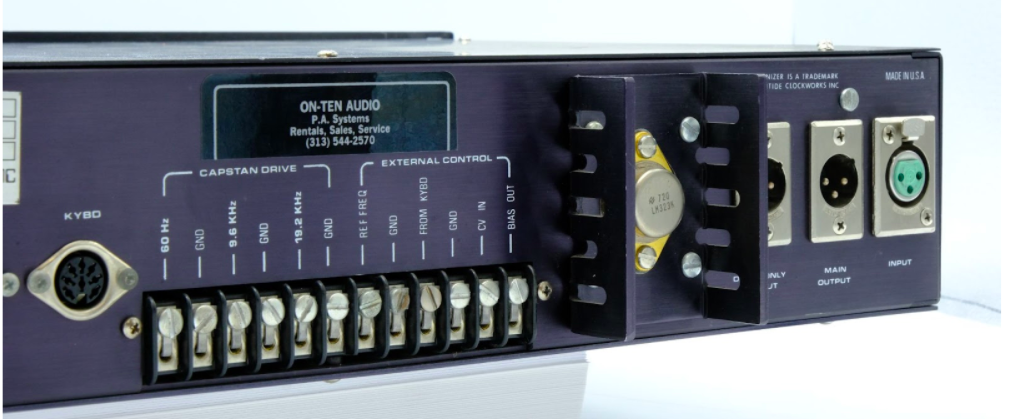
Now that you know all the ins and outs of the H949’s buttons and knobs, we will surface from this deep dive by the nerd who designed it (pictured here running his voice through an H949):
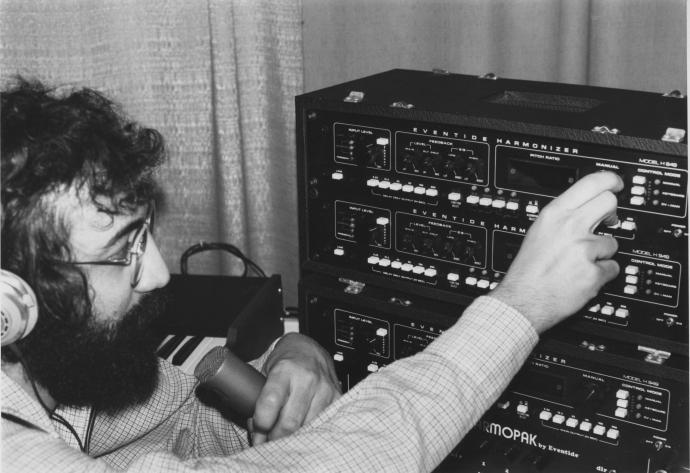
Stay tuned for 7.3 to hear from a few of the folks that found inspiration in this new sonic frontier!
Discover more from the pros:
- Suzanne Ciani on the Gear Club Podcast
- Professor Alex Case on the Gear Club Podcast
- Professor Alex Case’s website
Check out our previous flashbacks!
- Flashback #1: The Instant Phaser
- Flashback #2.1: The DDL 1745 Delay
- Flashback #2.2: The DDL 1745A Delay
- Flashback #2.3: The DDL 1745M Delay
- Flashback #3: The Omnipressor®
- Flashback #4.1: The H910 Harmonizer®
- Flashback #4.2: H910 Harmonizer® — The Product
- Flashback #4.3: H910 Harmonizer® — “Minds Blown”
- Flashback #5: FL 201 Instant Flanger
- Flashback #6: HM80 — The Baby Harmonizer®
- Flashback #7.1: The H949 Harmonizer®
- Flashback #7.2: H949 Harmonizer® — The New One
- Flashback #7.3: H949 Harmonizer® — Bending, Stretching, and Twisting Time
- Flashback #8: H969 Harmonizer®
- Flashback #9.1: Broadcast
- Flashback #9.2: Dump & Go – The Profanity Delay
- Flashback #10: Thinking Outside the Black Box